Understanding the Trick Parts and Repair Strategies for Product Packaging Maker Maintenance
Effective upkeep of product packaging machines rests on a detailed understanding of their crucial elements, including the structure, drive system, and securing devices. Recognizing usual upkeep problems, paired with the execution of preventative approaches and repairing methods, can substantially improve device dependability. The selection of repair work practices, including the use of OEM parts and the value of qualified service technicians, plays a crucial function in minimizing downtime. To absolutely understand the details of these systems and their maintenance, one have to consider the more comprehensive implications of ignoring these important methods.
Key Components of Packaging Makers
Product packaging equipments consist of several essential elements that interact to guarantee effective and effective packaging processes. At the core of these machines is the frame, which offers structural stability and houses the different operating components. The drive system, commonly a combination of electric motors and gears, promotes the movement of elements, making it possible for exact procedure throughout the packaging cycle.
An additional important element is the conveyor system, which transfers products with various stages of the packaging process. This is usually complemented by sensors and controls that check the position and speed of products, making certain synchronization and minimizing errors. The filling up system is important for properly giving the right quantity of item right into bundles, whether in liquid, powder, or solid form.
Securing devices, consisting of warm sealers or sticky applicators, play a crucial function in securing packages, stopping contamination and prolonging shelf life. Additionally, labeling systems are indispensable for providing needed product info, ensuring compliance with policies. Lastly, the control panel, equipped with straightforward interfaces, enables operators to take care of maker features, screen performance, and make modifications as needed, making certain ideal performance and effectiveness in product packaging operations.
Common Upkeep Concerns
Effective procedure of product packaging makers counts greatly on regular maintenance to prevent usual problems that can interfere with production. Among these problems, mechanical damage is prevalent, especially in parts like electric motors, seals, and conveyors, which can result in unforeseen downtimes. In addition, imbalance of components can result in inefficient operation, triggering items to be inaccurately packaged or harmed throughout the procedure.
Another common maintenance problem includes the build-up of dirt and particles, which can hinder the equipment's sensing units and relocating components. packaging machine repair service. This not just affects performance but can also position security dangers. Lubrication failures can lead to increased friction, resulting in overheating and ultimate part failing.
Electric issues, commonly originating from loosened connections or damaged circuitry, can disrupt machinery functions, resulting in significant manufacturing hold-ups. Finally, software application glitches due to inappropriate setups or outdated programs can prevent the equipment's operation, requiring immediate treatment. Attending to these typical upkeep problems proactively is vital for guaranteeing optimum efficiency and longevity of product packaging machinery.
Preventative Upkeep Techniques
Implementing preventative upkeep techniques is crucial for maintaining the efficiency and dependability of packaging makers. These strategies incorporate a systematic strategy to maintenance, concentrating on the regular assessment and maintenance of equipment to preempt prospective failures. By adhering to a set up maintenance program, operators can recognize wear and tear on elements prior to they result in substantial breakdowns.
Secret components of a preventative maintenance method consist of routine assessments, part, cleansing, and lubrication replacements based upon supplier recommendations. Using lists can simplify this procedure, ensuring that no vital jobs are overlooked. Additionally, preserving precise documents of upkeep tasks help in tracking the equipment's performance over time, helping with notified decision-making relating to future upkeep demands.
Educating team on the importance of preventative maintenance enhances conformity and fosters a culture of proactive care. Executing a predictive maintenance component, utilizing data analytics and sensor technology, can even more optimize equipment performance by anticipating failings prior to they take place.
Repairing Strategies
When encountered with malfunctions or inefficiencies in product packaging makers, utilizing systematic troubleshooting techniques is crucial for recognizing and solving issues swiftly. The initial step in effective troubleshooting is to develop a clear understanding of the device's operational criteria and performance metrics. This entails examining the device's requirements, in addition to any mistake alerts or codes presented.
Next, drivers ought to perform a visual inspection, inspecting for obvious indicators of misalignment, wear, or damages. This typically includes analyzing belts, gears, and sensors to pinpoint possible reasons for malfunction. Collecting functional data, such as manufacturing prices and downtime logs, can also supply understandings into persisting issues.
When possible problems are determined, making use of a logical technique to separate the root cause is critical. This might require testing private parts or systems in a regulated manner. Engaging in conversations with drivers that interact with the machinery routinely can generate valuable comments about unusual habits or patterns.
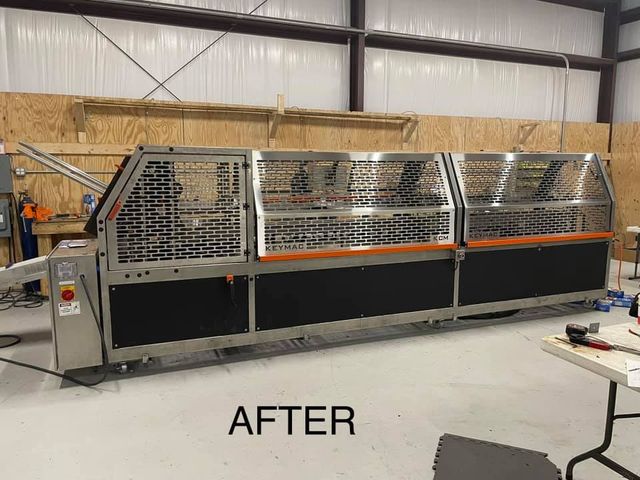
Repair Service and Substitute Ideal Practices
A detailed understanding of repair find service and replacement ideal techniques is crucial for preserving the longevity and performance of packaging review machines. Regularly analyzing the problem of device parts permits for prompt intervention, preventing even more considerable concerns that can cause costly downtimes.
When fixings are needed, it is important to utilize OEM (Original Devices Manufacturer) components to guarantee compatibility and efficiency. This not only maintains the integrity of the equipment however additionally supports service warranty contracts. In addition, it is recommended to keep an inventory of essential spare components to facilitate fast substitutes and reduce functional disruptions.
For complicated fixings, engaging licensed technicians with specialized training in packaging equipment is advised. They possess the experience to diagnose problems properly and execute repair work successfully. Furthermore, documenting all repair service tasks and parts replacements is important for keeping a comprehensive maintenance history, which can help in future troubleshooting.
Finally, carrying out a positive strategy, consisting of normal inspections and anticipating maintenance techniques, enhances the reliability of packaging devices. By adhering to these best practices, companies can guarantee ideal device performance, reduce operational risks, and extend equipment life-span.
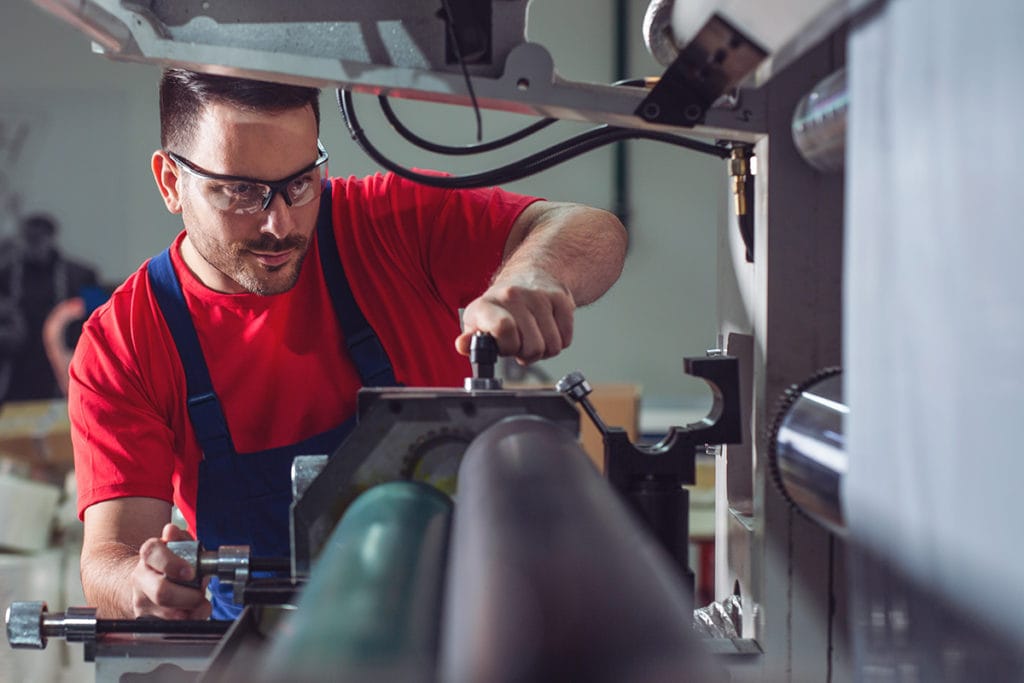
Conclusion
Finally, a detailed understanding of packaging machine elements and effective upkeep techniques is essential for ideal efficiency. Regular examinations and the use of OEM components can substantially minimize downtime, while a well-documented upkeep background promotes aggressive care. Utilizing certified service technicians further improves fixing quality and integrity. By implementing these methods, companies can guarantee the durability and performance of packaging makers, inevitably contributing to enhanced functional productivity and decreased expenses.
Effective maintenance of packaging devices hinges on a complete understanding of their vital parts, consisting of the structure, drive system, and visit the website securing devices.Reliable procedure of product packaging equipments counts greatly on normal upkeep to protect against usual concerns that can interfere with manufacturing.Carrying out preventative upkeep methods is important for sustaining the effectiveness and dependability of packaging machines. Additionally, keeping exact documents of maintenance activities aids in tracking the equipment's efficiency over time, assisting in notified decision-making concerning future maintenance needs.
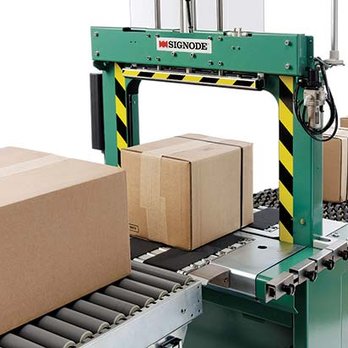